躍進・先進の夢を形にかえて・・・
より高度なものづくりを目指し、世界に先駆けた最先端技術の開発に取り組んでおります。近年では、新素材・新工法の開発や航空機部品製造等のトライアルも行っております。
アプセット鍛造
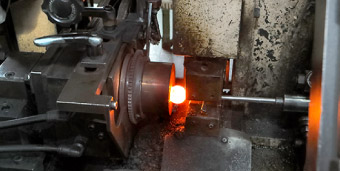
当社が独自に開発したアプセッターによる鍛造工法は、材料歩留まり、製品精度を飛躍的に向上し、高品質、低コストのエンジンバルブ生産を実現しております。
省エネルギー熱処理技術
40年前に自社製造連続調質炉によるエンジンバルブを主とした耐熱鋼部品の空冷焼入れ技術を開発、30年前には水溶性焼入剤による型打鍛造品の鍛造焼入技術を確立しました。省エネルギーと環境に配慮したこれらの熱処理技術は現代のスタンダードとして、日本中で行われております。
シングル段取りダイセット
ダイセットメーカとの共同研究により、シングル段取りダイセット(カセット交換方式)を開発しました。このシングル段取りダイセットはプレスダイセットの主流技術として、国内外問わず広く普及しております。
セラミック型
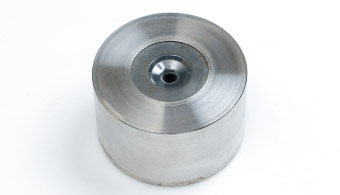
脆性材料であるセラミックの破壊を防止し、セラミックの特性を効果的に生かした耐久性の高い鍛造用金型を開発し、平成8年に特許化に成功しました。
日本塑性加工学会 技術開発賞「熱間鍛造用セラミックス型の開発」(H7.5.19)
放電プラズマ焼結(SPS:Spark Plasma Sintering)
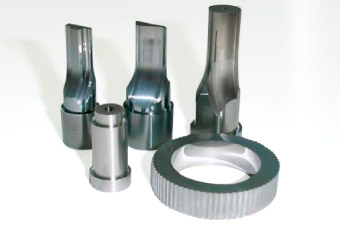
SPSを用いた超精密金型用の高硬度超硬合金の焼結技術を確立し、精密金型部品の超寿命化を実現しました。また、応用技術としてセラミックス材料の焼結や異種材料の接合などの受託研究を行い、各種研究開発のサポート事業に取り組んでまいりました。
※現在、放電プラズマ焼結は行っておりません。
Ni基超耐熱合金:EXEO-NF90
インコネル713CとSUS310Sの中間に位置する高性能かつリーズナブルなNi基超合金を素材メーカーと共同開発しました。耐熱性、耐食性に優れたバランスの良い新素材です。
高圧スライド加工法(HPS:High-Pressure Sliding)
HPSとは、共同研究を行う九州大学のグループが近年開発した材料の結晶粒を”超”微細化する最先端の組織改質技術です。この技術によって結晶粒を超微細化したAl合金やMg合金、Ti合金、Ni基超合金では、小さな力で極めて大きな変形が得られる超塑性現象が発現します。成形性を大幅に改善する組織改質技術と当社のコア技術である熱間鍛造技術を組み合わせることにより新次元のものづくりを実現します。
12th International Conference on Superplasticity in Advanced Materials(ICSAM)2015
Best Poster Award受賞(H27.9.9)
研究開発プロジェクト
- 国の戦略的基盤技術高度化支援事業(通称 : サポイン) (経済産業省)の採択を受けました。
平成21年度補正 「Ni基合金鍛造の高度量産プロセスの開発」 平成22~23年度 「Ni基合金鍛造の高度量産プロセスの開発」 平成25~27年度 「Ni基超耐熱合金の組織改質と高機能ターボ部品の開発研究」 平成28~30年度 「難加工材料の組織微細化と超塑性鍛造による最先端ターボ部品の新量産工法開発」
自動化・省力化機器の設計・製作
社内における自動化・少量化の課題を自ら設計・製作し解決すると共に、お客様のご要望にもお答えします。
●機械加工における自動計測+補正加工システムの開発
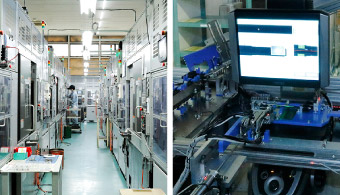
NC旋盤によるシャフト加工工程に於いて、加工ワークを自動搬送し加工後の振れ・外径・長さ寸法及びネジの有効径等を測定し、良品・不良品の選別を自動化するとともに、画像寸法測定により、測定データを加工機に自動でフィードバックし、補正加工を行い加工精度の向上と安定を図るシステムを自社において開発しました。
(詳細なシステム概要等)
●その他の自動化事例
- バリ取りロボット
- 軸受け圧入装置
航空機部品製造へのトライアル
●平成21年度補正予算事業「戦略的基盤技術高度化支援事業(通称サポイン)」(経済産業省)に採択され
「Ni 基合金鍛造の高度量産プロセスの開発」をテーマに、航空機エンジン部品の試作を行いました。
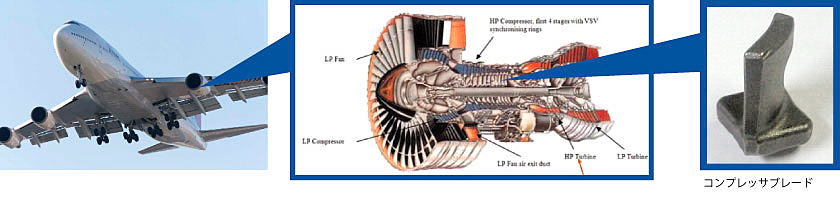
●平成28年度地域中核企業創出・支援事業「航空機エンジン部品加工トライアル」(経済産業省)の採択を受け航空機エンジン部品の試作を行いました。
●平成29年度長野県航空機産業中核支援事業加工トライアル(長野県)の採択を受けて、航空機部品製造に係る治具の試作を行う。